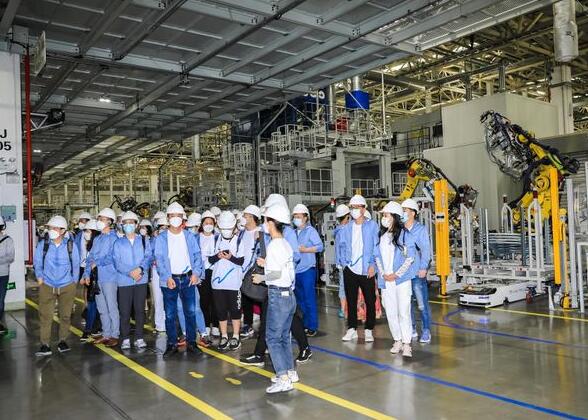
上1000臺機器人協同運作、關鍵工序100%自動化、24小時全時在線檢測……在賽力斯華為智選SF5首批用戶交車之際,上游新聞記者來到這款新車的誕生地——金康賽力斯兩江智能工廠,對這座以工業4.0標準打造的智能工廠進行了打探。
“真沒想到身邊還有這么先進的工廠,這么多工業機器人和自動化設備,完全顛覆了我對汽車制造的傳統印象。”一名重慶車主在參觀結束后,這樣對記者感嘆道。
兩江智能工廠以工業4.0為制造標準,以平臺化、自動化、智能化、數字化為目標,采用德國豪華汽車生產工藝,超1000臺機器人協同運作實現高度自動化,關鍵工序100%自動化,24小時全時在線檢測,有效降低人力成本的同時讓制造精度、產品品質達到超一流水準。
比如,為避免在超過300伏特高壓下進行電池包作業帶來的潛在危險,這座工廠的電池PACK車間內的生產模組由全自動 AGV 無人生產,關鍵焊接工序采用最先進的精密高速鋁絲焊接技術,實現了焊接全自動在線監測。
沖壓車間擁有整線防塵降噪、自動藍光測量系統、自動化裝箱、AGV自動傳輸、一鍵換模等先進技術及設備。全封閉高速同步機械沖壓線僅需5秒就可以沖壓完成一個部件。沖壓車間配備了目前世界上最先進的藍光檢測,檢測效率是傳統汽車工廠三坐標檢測的3-5倍,檢測精度也達到了0.05毫米。比一根頭發絲還要細,達到人工作業無法達到的精度。
焊裝車間內,生產線的上料、輸送、焊接、涂膠等工序全部實現自動化,焊接的自動化率達到100%。整條生產線的機器人達到319臺,配備多項當前行業頂尖工藝,如激光遠程飛行焊、視覺定位抓件、在線檢測等工藝。尤其是機器人遠程激光焊接技術,不僅讓汽車的焊縫更加美觀,同時具備焊接速度快、變形小的特點,更可以對作業空間小、焊鉗無法焊接的位置進行焊接。
涂裝車間則使用了奔馳、寶馬等汽車工廠同款成套設備。同時采用了世界先進的噴涂工藝和環保水性涂料,確保了車身的高品質油漆質量。車間使用的七軸噴涂機械臂,還是國內首條使用七軸機械臂的汽車生產線。與六軸機械臂相比,七軸機械臂更加靈活,便于末端執行器到達特定的位置,即便是車身死角,七軸機械臂噴涂也游刃有余。
在總裝車間,德國AFT公司提供的輸送線設備,實現了汽車前后擋風玻璃采用機器人自動涂膠和安裝,保證裝配質量;座椅采用機器人完成放置;輪胎、儀表臺也全部采用機器人安裝。其中有國內第一家總裝在線外觀間隙面差檢測機器人,它通過跟蹤確定動態車輛的實時位置,由機器人自動完成相關檢測,其檢測精度高達±0.04mm。
不難看出,作為賽力斯華為智選SF5的誕生地,重慶兩江智能工廠為這款新品注入了高品質的制造基因。