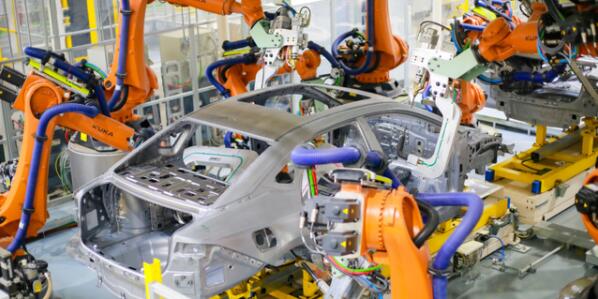
胡林是廣汽埃安新能源汽車有限公司制造部焊裝車間的一名管理人員。他平時(shí)的工作就是與各種車身結(jié)構(gòu)件、覆蓋件打交道,這些部件來自沖壓車間,在焊裝車間完成焊接變成白車身,然后再被運(yùn)送到涂裝車間。在他帶領(lǐng)的小團(tuán)隊(duì)里,既有普通的焊裝工人,也有生產(chǎn)線上的機(jī)器人。
汽車制造工廠的生產(chǎn)流程,一般分為沖壓、焊裝、涂裝、總裝四道大工序,而焊裝這一步是被新技術(shù)改造較為徹底的一環(huán)?,F(xiàn)在,國內(nèi)大多數(shù)汽車工廠的焊裝車間都引入了焊接機(jī)器人,以人工作業(yè)為主的焊接方式早已成為過去式。近幾年隨著工業(yè)4.0和智能制造的發(fā)展,更多的數(shù)字、智能科技被應(yīng)用到汽車生產(chǎn)領(lǐng)域,傳統(tǒng)的汽車生產(chǎn)線正在經(jīng)歷著一場新技術(shù)的洗禮。
在記者的印象中,不少汽車工廠的焊裝車間都會(huì)出現(xiàn)“火花四濺”的場景,但在廣汽埃安的工廠內(nèi)卻很少有這種現(xiàn)象。胡林告訴記者,這是因?yàn)椴捎昧艘环N“冷金屬過渡焊”的技術(shù),通過對電流的短路控制實(shí)現(xiàn)無電流狀態(tài)下的熔滴過渡,抑制了“火花”,“這只是一個(gè)很小的技術(shù),體現(xiàn)出工廠節(jié)能環(huán)保的生產(chǎn)理念”。
廣汽埃安稱自己的工廠為“智能生態(tài)工廠”,作為一座專門生產(chǎn)電動(dòng)車的工廠,其與傳統(tǒng)燃油車工廠之間有著較大的區(qū)別。該工廠自2017年起開始建設(shè),2019年正式投產(chǎn),規(guī)劃總產(chǎn)能20萬輛。在過去一年多時(shí)間里,這里已生產(chǎn)出四款埃安品牌車型。今年11月,廣汽埃安宣布脫離廣汽新能源,從一個(gè)產(chǎn)品系列變成了一個(gè)獨(dú)立的高端智能純電品牌。
在這個(gè)面積并不大的焊裝車間里,忙的時(shí)候會(huì)進(jìn)行“多班倒”,即使這樣,要完全保障產(chǎn)能依然是一項(xiàng)頗具挑戰(zhàn)的工作。這對設(shè)備的連續(xù)穩(wěn)定性提出了很高的要求。此外,設(shè)備、人員、機(jī)器人之間能否高效配合,還取決于整體生產(chǎn)決策是否足夠智能。這一切都不是單純靠引進(jìn)國際先進(jìn)技術(shù)就能解決的,而是需要工廠根據(jù)自己的實(shí)際情況進(jìn)行創(chuàng)新。在對胡林的訪談中,他向記者談到了更多關(guān)于這座純電動(dòng)車工廠的“隱藏技能”。
生產(chǎn)線上的“虛擬現(xiàn)實(shí)”
到了數(shù)字化、智能化制造時(shí)代,焊裝工藝到達(dá)了一個(gè)什么樣的水平?
在胡林看來,數(shù)字化的一個(gè)重要應(yīng)用是模擬仿真技術(shù),這一技術(shù)實(shí)現(xiàn)了“虛擬現(xiàn)實(shí)”,全工序所有生產(chǎn)線通過搭建3D數(shù)字化模型,提前對焊槍可達(dá)性、線體節(jié)拍進(jìn)行可行性驗(yàn)證,進(jìn)行機(jī)器人離線編程及電氣程序虛擬調(diào)試,這樣的模擬仿真技術(shù)可以讓現(xiàn)場調(diào)試周期削減35%。
“和傳統(tǒng)燃油車相比,新能源汽車的電氣化程度更高,在智能模塊化裝配方面設(shè)計(jì)要求更加精確。”胡林表示。而要達(dá)到這一點(diǎn),先進(jìn)的工藝技術(shù)必不可少。胡林對生產(chǎn)線上應(yīng)用的技術(shù)如數(shù)家珍,隨口就說出了一大堆技術(shù)名詞:3D視覺引導(dǎo)技術(shù)、激光在線測量技術(shù)、鋼鋁混合柔性總拼技術(shù)、鋁點(diǎn)焊接壓力自適應(yīng)技術(shù),SPR(自沖鉚接技術(shù))、FDS(熱熔自攻絲螺接技術(shù))等連接技術(shù)。
據(jù)了解,廣汽埃安為實(shí)現(xiàn)車身輕量化,在車身材料和結(jié)構(gòu)上進(jìn)行了創(chuàng)新。在汽車行業(yè),有的品牌車型采用全鋁車身,而廣汽埃安車型采用“下鋁上鋼”的車身結(jié)構(gòu)。據(jù)介紹,這種結(jié)構(gòu)可以在保證品質(zhì)不受影響的前提下,讓車身減重25%,達(dá)到與全鋁車身相同的減重效果。
然而,鋼鋁連接本身是一個(gè)技術(shù)難題。傳統(tǒng)的同種材料連接采用電阻熔化焊,但由于鋼和鋁的電阻、熔點(diǎn)均不同,無法直接進(jìn)行電阻熔化焊。為解決這個(gè)難題,廣汽埃安采用了SPR和FDS技術(shù),SPR通過沖頭在鉚釘上加壓,使鉚釘進(jìn)入板材,鉚釘釘腳張開,與板件形成互鎖連接,從而實(shí)現(xiàn)鋼和鋁的穩(wěn)定連接;FDS則是通過在螺釘上施加向下的壓力和扭力,最終實(shí)現(xiàn)可靠的熱機(jī)械擰緊連接,不僅可實(shí)現(xiàn)鋼鋁不同板材之間連接,還可減少連接的限制條件實(shí)現(xiàn)單側(cè)連接。
“我們這是全球第一條實(shí)現(xiàn)鋼鋁柔性生產(chǎn)的生產(chǎn)線,且可兼容多款車型共線生產(chǎn),不同車型的切換生產(chǎn)最快可做到1分鐘完成。這在全球范圍內(nèi)擁有絕對的領(lǐng)先性。”胡林表示。
“用戶時(shí)代”的定制生產(chǎn)
“我認(rèn)為智能生產(chǎn)帶來了生產(chǎn)效率的有效提升,更關(guān)鍵的是滿足了消費(fèi)者的個(gè)性化需求,廣汽埃安智能生態(tài)工廠率先打造了全球領(lǐng)先的大規(guī)?;?dòng)式定制生產(chǎn)模式,引領(lǐng)汽車智造新變革。”胡林說。
以往的汽車生產(chǎn),都是廠家生產(chǎn)出商品再賣給消費(fèi)者,但現(xiàn)在消費(fèi)者的需求開始反向定義工廠生產(chǎn)。根據(jù)用戶的個(gè)性化需求提供制定生產(chǎn),也不再是少數(shù)豪華品牌的專屬,現(xiàn)在很多中高端新能源品牌均將其視作重點(diǎn)角逐的領(lǐng)域。同時(shí),定制化也不再是小規(guī)模,而是朝著大規(guī)模發(fā)展。但大規(guī)模定制化生產(chǎn)意味著種類繁瑣的零部件都能夠被準(zhǔn)確定位、運(yùn)輸和裝配,零部件的廠內(nèi)搬運(yùn)、物流成了關(guān)鍵所在,而這催生了AGV(AutomatedGuidedVehicle,智能搬運(yùn)機(jī)器人)。如何實(shí)現(xiàn)智能搬運(yùn)機(jī)器人的有序無誤操作,將其與人員、設(shè)備之間緊密配合,對工廠來說是一個(gè)很大的考驗(yàn)。
據(jù)了解,智能搬運(yùn)機(jī)器人的傳統(tǒng)導(dǎo)航方式通過地面埋設(shè)金屬線實(shí)現(xiàn)電磁導(dǎo)航,但廣汽埃安總裝車間的AGV導(dǎo)航采用磁帶導(dǎo)航,即通過在路面上貼磁帶替代在地面下埋設(shè)金屬線,由磁帶感應(yīng)信號實(shí)現(xiàn)導(dǎo)引。“磁帶導(dǎo)航的定位精確,靈活性比較好,磁帶鋪設(shè)也相對簡單,改變或擴(kuò)充路徑較容易,導(dǎo)引原理簡單而可靠,便于控制通訊,對聲光無干擾,投資成本比激光導(dǎo)航低很多。”胡林介紹。
工廠內(nèi)部的定制化生產(chǎn)只是完成了第一步,接下來還要將之與用戶的個(gè)性化需求對接起來,才算形成了完整的定制化生產(chǎn)閉環(huán)。據(jù)了解,廣汽埃安開發(fā)了一個(gè)專屬APP來完成消費(fèi)者需求收集。消費(fèi)者通過APP可以在任何地方開始定制并下單,然后用戶的所有需求信息將同步到工廠及全球供應(yīng)商。“也就是從用戶點(diǎn)擊購車下單那一刻開始,零部件已經(jīng)進(jìn)入生產(chǎn)流程,省去以往各種單據(jù)傳遞的環(huán)節(jié),效率快的不是一點(diǎn)點(diǎn)。為了準(zhǔn)確掌握每個(gè)零部件送達(dá)工廠的時(shí)間,我們采用大數(shù)據(jù)對每個(gè)零部件進(jìn)行排產(chǎn)跟蹤,甚至把運(yùn)輸過程中可能遇到的天氣影響及交通擁堵時(shí)間都計(jì)算在內(nèi),力求讓零部件到位時(shí)間精準(zhǔn)到秒。”胡林說。
被數(shù)字改變的工作方式
“科技一日千里,工人也得堅(jiān)持學(xué)習(xí),以適應(yīng)先進(jìn)機(jī)器的升級迭代。”談到智能科技對工人工作方式的影響時(shí)胡林這樣說。
為適應(yīng)技術(shù)時(shí)代的生產(chǎn),工廠對工人的培訓(xùn)要求變得更高。廣汽埃安每月有多場技能培訓(xùn),持續(xù)提升工人的生產(chǎn)技能水平,其中主要以智能機(jī)械的實(shí)操培訓(xùn)提升為主,但也包括傳統(tǒng)手工技能的培訓(xùn)及安全生產(chǎn)的培訓(xùn)。在考核方面,一般會(huì)從工作效率和工作質(zhì)量方面進(jìn)行符合標(biāo)準(zhǔn)的設(shè)定,標(biāo)準(zhǔn)每年會(huì)有相應(yīng)的提升,從而實(shí)現(xiàn)生產(chǎn)效率持續(xù)提升。
目前有一種觀點(diǎn)認(rèn)為,隨著智能AI設(shè)備的大量應(yīng)用,工廠對工人的需求會(huì)減少,這對基層工人而言是一個(gè)不利的消息。但胡林認(rèn)為,這種觀點(diǎn)不完全正確,雖然智能化和自動(dòng)化技術(shù)減少了作業(yè)崗位,但解放出來的工人可以從事更多創(chuàng)新型工作。例如,用來保全機(jī)器的人員數(shù)量就比以前增加了。
當(dāng)被問到是否對自己制造的產(chǎn)品抱有信心時(shí),胡林表示“那當(dāng)然”。他認(rèn)為,廣汽埃安的生產(chǎn)方式背靠廣汽集團(tuán)30多年的產(chǎn)業(yè)積累,并結(jié)合了大數(shù)據(jù)、人工智能等先進(jìn)科技,做到了高質(zhì)量、高效率和短交期。工廠在鋼鋁車身柔性生產(chǎn)、數(shù)字化自主決策、互動(dòng)式定制、能源綜合利用四大方面有著全球領(lǐng)先的優(yōu)勢。“廣汽埃安整個(gè)工廠沒有一個(gè)燃油儲(chǔ)罐,在全球范圍內(nèi)僅有特斯拉和廣汽埃安能做到這點(diǎn)。”胡林表示。作為自主高端智能純電品牌的一員,廣汽埃安的競爭對手直指特斯拉。
(應(yīng)采訪對象要求,文中“胡林”采用化名)